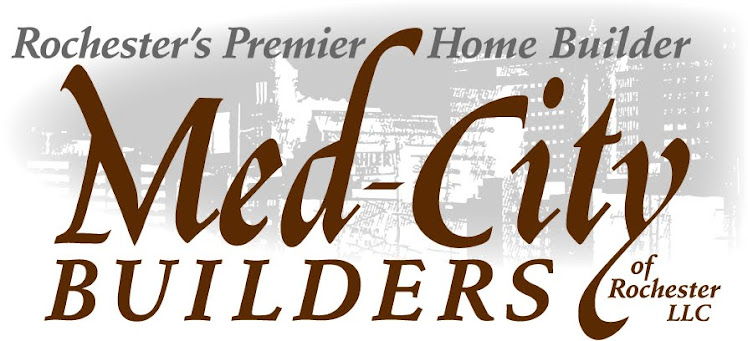
Tuesday, December 13, 2011
Would you pay 1% more to have your entire home be 100% American Made?
I recently read about and watched a report on ABC News about the effects on our economy of buying American Made products for building new homes. They stated, if all home builders in our country bought just 5% more American made products than before, we could generate some 250,000 new jobs in our country. I currently use many of the products on the list ABC published, but was looking for feedback for our own region on if buyers would be willing to pay the 1% difference in price they discussed if I used ALL American made products. I really would appreciate your feedback. I plan on making a conscience effort to purchase more American made goods regardless, but would love to hear your feedback. I will post this on Facebook as well and would appreciate your input!
Tuesday, November 29, 2011
Should we drain our water heater???
I know many of my past customers use this blog as a tool for making their homes more efficient. During all of my final walk throughs, 30 day walk throughs, and even the one year walk through with my past customers I mention emptying their water heater yearly. While most don't ever even touch this appliance once it is turned on, there are some very inexpensive things we can do to make it last much longer than the typical life expectancy. To drain your water heater, simply turn the switch to the unit off. It is typically located near the floor where you would also adjust the temperature. Once it is shut off, find the main line of water into the water heater. This is located just above the water heater usually. Now that the power and the water source is off to the unit, attach a garden hose to the screwed outlet on the water heater. Once the hose is attached and ran to the floor drain, take a flat head screw driver and use it to open the valve next to the screwed outlet. It typically doesn't take long to drain the water out, but by doing it this way the sediment on the bottom of the water heater leaves as well as the water. This sediment is typically what accumulates over time and will eventually cause the water heater to rust from the bottom. Once the water heater is drained of the water, screw the valve closed completely. Then open the water valve on the top of the water heater back up to fill the unit up. Remember not to turn the water heater on before any of this. Doing so can damage the water heater due to how fast the elements can heat up. Once the unit is filled and no water is leaking from the valves, turn on the water heater switch to start the heating of the water once again. This is really that simple to do and it will more than likely add years of worry free operation to your homes water heater.
Monday, October 24, 2011
Wait till spring or start now?
Simple question and most would say waiting till spring is the right answer. I can't totally disagree with them either, but we are in the perfect storm right now. Building costs and labor costs have been suppressed for years now and the pent up demand is starting to build in our industry. I have first hand seen the costs starting to tick up the wrong direction for the homeowner looking to build down the road. While waiting till spring has his merit, the idea of an interest rate going from the low 4% range even to a 6% range decreases a buyers buying power by tens of thousands of dollars. I also wrote blogs in the past discussing the ideas of the materials being so much dryer in the fall and winter months. Come spring the materials have had a chance to gain moisture from the snow and the increasing humidities in the air. This is the first cause of a home seeing nail pops and sheetrock cracks. I monitor the homes I build a year after they are completed and have definitely noticed a difference on the homes we start in the fall vs spring. The fall homes have much less movement and much less for cosmetic cracks over time. That all being said, I'm not against spring building. It is obviously the busiest time of the year for me. I just don't want to see someone miss out on a valuable opportunity when while we are sitting in the eye of this perfect storm. Call or email your requests today!!
Wednesday, September 21, 2011
We are rolling again!!!
I just wanted to drop a line to all my past customers and friends for their support over the past few years. It has been a struggle in this business and I have managed to stay busy with all of your support. We just dug one basement for an expanding family in NE Rochester getting ready for twins!! I am just finishing up with a large project in the metro area of Lake Elmo and hope to post some finished pictures when completed next Friday. 6400 sq ft fully finished home on an acreage and finishing on the day we scheduled 5 months ago! We have 5 more to dig prior to the fall rush and hope to have several more to start before the snow starts to fly. One of our projects is going to be in Northfield on the Country Club golf course there. Should be a fun project and a super couple to work with. Another home to start is in NE Rochester for a couple expanding their business and getting closer to their family. It is a gorgeous Ranch on a super lot in Shannon Oaks. We then plan on digging a home for another expanding family in ManorWoods west of Rochester. We are just getting going on the selections and should be digging by mid October. We should be starting another home in NW Rochester sooner than the homes listed above. Another up and coming family who is currently getting all their new home selections dialed in for us to roll along. Lastly, we are looking at a larger 2 story in SE Rochester for a developer. This home would be a great home for any family looking to expand and will be ready for a move in by the time the snow would start to fly. I really do appreciate all of your support and hope the summer found you all some fun family times. Drop us a line anytime here with thoughts and ideas you have. We are all ears and appreciate the feedback!!!
Wednesday, September 14, 2011
Is Fall a good time to build a home???
I have heard many of my clients express concerns about building too late in the fall or winter. I have built a few hundred new homes in the Rochester and Surrounding communities and meet with my clients at the one year point of when we closed on their new home. I do this to not only meet up with my past customers, but also to gauge how the home we built reacted over the past year. One of the surprising things I have found is that the homes we build through the winter actually show much less movement than the ones we build in the spring. There are a couple factors attributed to this I believe. First, all the raw materials going into the home are at a point where they are the driest point of the entire year. The humidity is virtually gone in the fall and winter months. Secondly, I feel with the lowered humidity the home doesn't actually take on moisture while we are building. When wood takes on moisture, it swells. If this wood doesn't dry out prior to the vapor barrier going on or the sheetrock, it is much more likely to cause nail pops and sheet rock cracking over the next year. Building in the fall and winter can have its challenges as well. Heating costs may be higher, but due to the fact we are able to build these homes in a 2 to 4 month window we don't see that as much of a factor in our homes. The bottom line is that potential clients should not have concerns about building in the winter months if the builder they choose is capable of handling the conditions that come with it. You might be surprised how well the home will function for you if you do!
Wednesday, June 22, 2011
Does Your Builder Come Highly Recommended?
I am sure you have all heard horror stories about how time consuming, expensive and stressful building a new home is. That doesn't have to be the case! Building a new home can be fun, easy and within budget! Plus you get your dream home with everything YOU want! The key is to pick the right builder. As a builder, it is our job to figure out all of the small details and put it together...basically taking the stress off your shoulders!
The best recommendations you can receive about a builder are from past clients. They have been through the process and can honestly tell you their first hand opinion and experiences. This is why when we meet with prospective clients, we include a reference list along with a letter of recommendation. We encourage our clients to check up on us. Whether you are building or buying a house, it is a big event in every person's life, so it is important to us that our clients feel comfortable with their choice and are confident in our work and service.
I have included a recommendation letter from a client that recently built a new home with us.
We would love to hear what you expect out of your builder, whether you are thinking about building, currently building, built in the past or have never thought about it! We look forward to hearing from you!
Monday, May 23, 2011
Our Best Energy Star Rating Yet!
We have posted in previous blogs about the Energy Star Rating and what that means for both us as a builder and our clients. We recently completed a home and got the best score to date, which is 26 points above the Energy Star standards! For more information on Energy Star, visit http://www.energystar.gov/.
Tuesday, April 26, 2011
Win Dinner for 6 at Osaka AND a Toys R Us Gift Card!!!
As you may have read in a previous post, we are giving away Dinner for 6 at Rochester's new Osaka Sushi & Steakhouse. In addition, we have decided to add a $100 GIFT CARD TO TOYS R US!
Heres how you can win BOTH!
Come and visit us during the Rochester Area Builder's Parade of Homes at 1121 Maplebeck Enclave, Byron (Somerby Subdivision) during the showtimes listed below and pick up a floor plan for you and/or your child to draw your dream floor plan. If your child enters his/her drawing, you and your child will be eligible to win the Dinner for 6 AND the Toys R Us gift card!
Parade Times:
Saturday, April 30th 12:00p.m.-5:00p.m.
Sunday, May 1st 12:00p.m.-5:00p.m.
Saturday, May 7th 12:00p.m.-5:00p.m.
Sunday, May 8th 12:00p.m.-5:00p.m.
And remember, entries will be voted on our Med City Builders of Rochester, LLC Facebook Page.
Please see our previous blog, dated April 12, for additional entry information.
Heres how you can win BOTH!
Come and visit us during the Rochester Area Builder's Parade of Homes at 1121 Maplebeck Enclave, Byron (Somerby Subdivision) during the showtimes listed below and pick up a floor plan for you and/or your child to draw your dream floor plan. If your child enters his/her drawing, you and your child will be eligible to win the Dinner for 6 AND the Toys R Us gift card!
Parade Times:
Saturday, April 30th 12:00p.m.-5:00p.m.
Sunday, May 1st 12:00p.m.-5:00p.m.
Saturday, May 7th 12:00p.m.-5:00p.m.
Sunday, May 8th 12:00p.m.-5:00p.m.
And remember, entries will be voted on our Med City Builders of Rochester, LLC Facebook Page.
Please see our previous blog, dated April 12, for additional entry information.
Tuesday, April 12, 2011
Win A Dinner for 6 at Osaka Sushi & Steakhouse!!!
We will be giving away a dinner for 6 at the new Osaka Steak and Seafood. You can design your own floor plan and your group along with your friends and family can vote for you to win. Pick your 6-person group that you'd like to enjoy drinks, appetizers, steak and/or seafood, and dessert with. Print it out the floor plan and submit your drawing.
To Be Eligible, You Must:
Ø Complete your customized plan and submit to Med City Builders of Rochester, LLC. The only restriction is to use the plan we provide, otherwise, it is yours to be creative with!
o Email to jenni@medcitybuilders.com
o Mail or drop off to
§ 2518 Superior Dr NW, Suite 103
Rochester, MN 55901
Ø Visit our website, www.MedCityBuilders.com and “Like” our Facebook page
Ø The finalists will be posted on our company’s Facebook page. The winner will be determined by how many “likes” each finalist receives.
Ø Encourage friends and family to vote “Like” for the winning picture!
Ø Pictures must be submitted by May 16, 2011. Voting will be open May 17, 2011 – May 23, 2011 at Noon.
Ø The winner will be posted on our website, Facebook, and our blog.
Tuesday, April 5, 2011
Why Spray Foam Insulation?
Spray foam insulation is a common word used in the building industry, but still not as readily used in our market. There are typically 2 types of spray foam used today. One is an open cell foam insulation and the other is a closed cell foam insulation. I will spend my time discussing the closed cell products.
Many of my clients begin discussing things they'd like to do in a home to make it a "Greener" home. Often I hear of possibly using geo thermal heating systems, solar panels, and even wind to power their homes. Once price is discussed these items often get pushed back on the wish lists either due to the cost or the fear of appraisals not being able to be achieved. Appraisers need to form an opinion of the property by the homes around it. If it is the same home as the neighbors, but has a $40,000 geo-thermal heating system in it they feel most buyers are not willing to pay that difference. Therefore the appraisal will come in less than needed to complete the project and the difference needs to be covered in the form of cash by the homeowner. At this point, I typically discuss spray foam to allow them to enhance the homes efficiency and do so without spending an excess of money. Often, I can spray foam a homes sidewalls for $3000 to $5000 more than a typical fiberglass insulated home. This is a workable number for appraisals and one that can typically be included in the price of the home without outlaying additional cash from the homeowner. The biggest difference in the way spray foam acts vs typical fiberglass insulation is the removal of air movement between the interior and exterior of the homes wall which I will call the stud pocket. I tell people that there are 3 ways heat is gained or lost. It happens through conduction, convection, and radiation. Radiation typically occurs through the windows of a home, while conduction occurs through the pass through of walls. The best way to describe conductions path of heat transfer is when you put a metal rod in the fire. You will burn your hand if you hold on to the end that is not in the fire eventually. The last way is convection. With spray foam insulation, convection has a difficult time occurring because we fill the entire stud pocket with the foam. Often people can feel air movement in the outlets of homes built in the past. This is typically not the air directly from the outside, yet the air spinning in the stud pocket behind the sheetrock. In the winter, the homes internal wall temp is around 70 degrees so the air in the stud pocket starts to rise. As it gets to the top, the air hits the outside wall where the temp can be minus 10 degrees so it begins to drop. The more dramatic the temperature difference between the two surfaces, the faster the air spins in the wall. This is why a typical fiberglass insulated wall actually loses R-value as the temperature difference increases. A home with an R-value of R-19 is based on the fact there is only a 10 degree temperature difference between the inside of the home and the outside. This is where closed cell spray foam shines. If we fill that entire stud pocket with something that does not allow any air movement, we eliminate one of the three ways heat can be transferred in the home. R-values on spray foam homes stay very stable despite the temperature changes. It does 2 other great things as well. It strengthens the outside walls and it makes for a much quieter home in the inside. I have talked in depth about the Energy Star ratings on homes and the one thing I'd like to mention is that our homes Energy Star ratings don't differ that much when we use one type of insulation or the other. We are still able to build an extremely tight home with fiberglass insulation. The true benefit comes through the energy bills my clients receive, although I don't have a true idea on the payback that each home will receive. If I spend $5000 extra to put spray foam in and it performs like I've mentioned above, the payback is much easier to achieve than a $40,000 Geo-Thermal heating system. I hope this helps you better understand the homes possible insulation systems.
Tuesday, March 29, 2011
Med City Builders of MN????
Just a quick heads up to let you all know I do plenty of traveling for clients looking outside the Rochester area. Over the past few years I have spent time building cabins in NW Wisconsin, a home in St Boni which is located on the west side of the Twin cities, will be building a large custom executive home in Northfield this spring, and am soon to be starting a very large executive custom home in Lake Elmo which is located in the NE part of the Twin Cities. I appreciate all of the referrals in the Rochester area my clients have passed my way, but wanted to extend the range of my company to all of you. I still send the same crews to the job sites which allows me to control the timelines, selections, as well as the superior workmanship my clients have grown to expect. If you or someone you know is looking outside the area, feel free to drop me a line. I'm happy to gas up the Med City Builders truck and take a drive!!
Thursday, March 24, 2011
Win a full course dinner for 6 at Osaka Seafood and Steak!!
Win Dinner and drinks for 6 at the new Osaka Steak and Seafood! We will be in the Spring Showcase of Homes coming up, so we will get updates on the times and dates soon. During the Showcase we are planning on another contest, but this one is for the adults. A Design Your Dream Home contest where we will give you the blank floor plan and you can submit your best home layout. We will be voting for the winners on Facebook like we did before with the Coloring Contest. We plan on giving away a 6 person appetizer, drinks, dinner, and dessert at the Osaka Steak and Seafood located at the old West Fire Grill in Rochester. I tried it for a trial run and it was some of the best food I've eaten!!! I hope to see you at the Showcase and email us if you can't so you too can get your floor plans to submit.
Monday, March 21, 2011
Custom Home Building
This is a term that is used pretty loose in our industry and can mean many things to many people. To some a custom home is one that is simply modified from an existing floor plan. To others a custom home is one that is created from just its most basic level in just thoughts to the final product. Custom home building in Southern MN takes on many other aspects as well. Whether or not to incorporate energy saving ideas or not and how to orientate a home to achieve the most desired result. Selecting a builder that allows you to explain your ideas and that listens to what you want vs what they might want is a tough choice for some people. One of the biggest obstacles I face day in and day out is to determine what people are trying to say when they are really not saying what they want. That has come from helping many clients design many homes and many hours up front with them figuring out how they wanted to get there. It happens during the design process and many times through the selection process. One of the biggest tips I can give any of my clients is to trust your gut feelings. I have taken many clients full circle only to end up doing exactly what they thought they wanted in the beginning. A true custom home builder's job is to make this idea a reality for you no matter what level of custom you feel you are on. Call anytime to get your dreams set in motion!!
Tuesday, March 15, 2011
Attention Air Exchangers!!!!
Depending on the price points needed to be attained by my clients, I include Air to Air Exchange units as often as I can. On average, I install them in 85% of the homes I build. The clients I build homes for have these systems explained to them them several times during our many walk throughs, but as we all know our lives take over and we forget what we should be doing with them once we are in the home. One of the first things I try to make clear is the air exchanger is actually the diamond shaped center core inside the box hanging from the ceiling. The box around it has a fan that makes the center air exchanger an active system. That center core is where the heat is extracted from the warm moist air leaving the home and where it blends with the cold air coming in. This is the reason for the 2 screen filters on the unit. Once filter or screen is for the air coming in and one filter or screen is for the air going out. Both air flows have dust in them and both need to be filtered so they don't dirty the center core or air exchanger. By keeping the 2 screens around the center core or air exchanger clean, it will allow the system to do what we installed it for. If these screens get dirty, the air cannot go through the air exchanger as easily and it also can potentially clog it. To clean the screens, simply open the door on the unit and remove it. Then slide the two screens off the center core and tap out the dust or soak them in hot soapy water if very dirty. Make sure they are dry before installing them onto the center core or air exchanger and vacuum out any other dust you might see in the housing around the center core. This should be done at least monthly or whenever you change your furnace filter.
Once a year, I recommend removing the center core and soaking that in hot soapy water as well. Fall is a great time to do this just prior to turning the system on for the winter months. I described the running schedule in an earlier blog. Again, make sure this core is dry before putting it back into the housing. At this same time, I recommend cleaning the intake screen at the exterior of the home. The air exchanger will run in the summer months and will be bringing on dusts when running the bathroom controls to remove moisture. This is the reason fall is a good time to clean the filter to make sure the air coming into the homes air exchange unit is cleaned before it even gets to the unit.
One of the most important things to keep in mind with these systems is that they work best when kept clean. It is impossible for you to expect a dust free home if the appliance in your home responsible for bringing in the fresh air is clogged. A little bit of maintenance goes a long ways with these types of systems. They are designed for making a home more efficient, but one of the most beneficial things they do is cut down on air born allergens. If you keep it clean, your home will be healthier and greener!!!
Once a year, I recommend removing the center core and soaking that in hot soapy water as well. Fall is a great time to do this just prior to turning the system on for the winter months. I described the running schedule in an earlier blog. Again, make sure this core is dry before putting it back into the housing. At this same time, I recommend cleaning the intake screen at the exterior of the home. The air exchanger will run in the summer months and will be bringing on dusts when running the bathroom controls to remove moisture. This is the reason fall is a good time to clean the filter to make sure the air coming into the homes air exchange unit is cleaned before it even gets to the unit.
One of the most important things to keep in mind with these systems is that they work best when kept clean. It is impossible for you to expect a dust free home if the appliance in your home responsible for bringing in the fresh air is clogged. A little bit of maintenance goes a long ways with these types of systems. They are designed for making a home more efficient, but one of the most beneficial things they do is cut down on air born allergens. If you keep it clean, your home will be healthier and greener!!!
Tuesday, March 8, 2011
Block walls or Poured walls and my 2 cents...
Earlier on this past month I discussed the concept of doing ICF foundations and how they rate on an efficiency scale. I mentioned my preference was not to use them and I preferred using a foundation wall construction that consisted of an exterior foam insulation design. There are a few ways we can construct foundation walls on new homes when we decide to move that insulation to the exterior. I commonly use two of them, block walls and poured walls. Both wall designs have their benefits.
The first one I will explain is the block foundation wall. We use the same type of footing depending on the plans designs for each of the wall designs. With a block wall, we can typically install them much faster than a poured wall. Layers or courses of block are added to achieve the desired ceiling height. Typically a 12 course block wall will give you an 8' ceiling when finished. A 13 course wall will give you an 8'6" finished ceiling height, and a 14 course will give you a true 9' ceiling height. Depending on the size of the home, a block wall can also save you money over a poured wall. Where they get their strength is from the open cores in the block we add steel rods to and pump them full of concrete. This is called core filling. This is also where the loads from the upper floors are transferred to the footing below the block wall. Block walls are very strong and have very few problems associated with them when backfilled properly.
Poured walls are the next wall I will discuss. Again, we use a footing similar to the block wall to begin setting up forms to design the poured wall. These forms allow us to build the walls to any desired height since we can regulate how much concrete actually goes in the forms. Prior to pouring the concrete, we add steel rods both vertically and horizontally. This attribute is what truly gives the poured walls the added strength over the block wall. When a load is being passed from the upper floors of the home to the foundation, it is transferred evenly over the footing instead of bearing on specific core filled points. Keep in mind when I say stronger, that doesn't mean a block wall will function any differently when we are completed. The concrete is then poured and cured in the form. Once cured, the forms are stripped from the concrete and we are left with the poured wall.
Both wall constructions allow us to work with Pre-stressed garages and both are capable of working with throughout most of the calendar year. If you have any thoughts or topics you'd like discussed in the future, feel free to drop us a line through our Facebook page or Website. Thanks for reading and heres to a super 2011!
The first one I will explain is the block foundation wall. We use the same type of footing depending on the plans designs for each of the wall designs. With a block wall, we can typically install them much faster than a poured wall. Layers or courses of block are added to achieve the desired ceiling height. Typically a 12 course block wall will give you an 8' ceiling when finished. A 13 course wall will give you an 8'6" finished ceiling height, and a 14 course will give you a true 9' ceiling height. Depending on the size of the home, a block wall can also save you money over a poured wall. Where they get their strength is from the open cores in the block we add steel rods to and pump them full of concrete. This is called core filling. This is also where the loads from the upper floors are transferred to the footing below the block wall. Block walls are very strong and have very few problems associated with them when backfilled properly.
Poured walls are the next wall I will discuss. Again, we use a footing similar to the block wall to begin setting up forms to design the poured wall. These forms allow us to build the walls to any desired height since we can regulate how much concrete actually goes in the forms. Prior to pouring the concrete, we add steel rods both vertically and horizontally. This attribute is what truly gives the poured walls the added strength over the block wall. When a load is being passed from the upper floors of the home to the foundation, it is transferred evenly over the footing instead of bearing on specific core filled points. Keep in mind when I say stronger, that doesn't mean a block wall will function any differently when we are completed. The concrete is then poured and cured in the form. Once cured, the forms are stripped from the concrete and we are left with the poured wall.
Both wall constructions allow us to work with Pre-stressed garages and both are capable of working with throughout most of the calendar year. If you have any thoughts or topics you'd like discussed in the future, feel free to drop us a line through our Facebook page or Website. Thanks for reading and heres to a super 2011!
Thursday, March 3, 2011
Special thanks
I just wanted to put out a special thanks to all of the super artists in this years coloring contest. I plan on doing more of this throughout the upcoming year, so stay tuned. It was a huge success for us, considering we did the entire contest through Facebook. I expected the family members to get on board with their children, but didn't think it would escalate like it did. We now have well over 200 "Likes" to our page and hope that will continue to grow as you all tell your friends and family about my company. Thanks again and I will get back to a more construction orientated blog next week.
Thursday, February 24, 2011
Afraid of the unknown??
Many peoples mis-conception of the building process makes them fear the unknown of what to expect in the building process. I often tell my clients that building a new home with a good builder is like buying an existing home that just doesn't exist yet. While the process of making selections can be overwhelming to some, others find this process completely enjoyable. You are able to make the home as personalized as you'd like. I personally make myself available as well to guide you through that part of the process.
Another fear I'm sure potential building clients have is the fear of cost overruns. When I start the process of working with clients, I try my best to pre-qualify them to know what they are looking for in their dream home. I have built many homes and have a firm grasp on what the amenities you are looking at will cost. This gets us very close to a final price. Before I even have my clients sign agreements to build, I take them on this guided tour I mentioned above. This alone pin points the costs on the home and allows us all to write an agreement that is detailed and extremely accurate. I average less than 2% in overages on all the homes I build and that is from the time we sign contracts to the time the home is completed. Most clients building homes worry about the horror stories that say they can expect 10 percent along the way in over runs. This simply doesn't occur with my company. Once the selection process is complete, my clients can enjoy the building process and watch all the hard work we all did come together. This too allows us to run a much tighter schedule.
I hope this helps explain the ways in which I can minimize your fears in the building process. My clients testimonials are the best way to ensure what I've said is the way I truly run my business.
Another fear I'm sure potential building clients have is the fear of cost overruns. When I start the process of working with clients, I try my best to pre-qualify them to know what they are looking for in their dream home. I have built many homes and have a firm grasp on what the amenities you are looking at will cost. This gets us very close to a final price. Before I even have my clients sign agreements to build, I take them on this guided tour I mentioned above. This alone pin points the costs on the home and allows us all to write an agreement that is detailed and extremely accurate. I average less than 2% in overages on all the homes I build and that is from the time we sign contracts to the time the home is completed. Most clients building homes worry about the horror stories that say they can expect 10 percent along the way in over runs. This simply doesn't occur with my company. Once the selection process is complete, my clients can enjoy the building process and watch all the hard work we all did come together. This too allows us to run a much tighter schedule.
I hope this helps explain the ways in which I can minimize your fears in the building process. My clients testimonials are the best way to ensure what I've said is the way I truly run my business.
Tuesday, February 15, 2011
Are ICF foundations better that others???
First of all, I'd like to say thanks to all who came out to the Rochester Area Builders Home Show this past weekend. It was a huge success and we had excellent traffic. In last years show, I built 2 custom homes for clients I met at the event. I hope to duplicate that this year and it is really looking positive with the feedback from the potential clients we met there.
One of the many topics this year that I had come from the people visiting my booth was regarding ICF foundations. Although many opinion may differ, they are not my choice for a couple reasons. The first being the added cost to the homeowner. In todays environment with appraisals being so difficult, this can be a factor right out of the gates for people. If the cost of the home is higher than the appraisal, other parts of the home need to be sacrificed in order to get the ICF's into the budget. The other problem I have with them is the mis-information on the efficiency. I think they are a great way to make a home efficient if they are taken all the way to the roof trusses(this is an extremely expensive way to use them), but if they stop at the foundation they are not. The State of MN has conducted studies proving that having more than R-5 insulation below grade is not necessarily a good thing. In MN, the average ground temperature is near 55 degrees all the time as long as it is below the frost line. 55 degrees can be good in the summer or the winter. I think of it this way. If in the summer it is 100 degrees outside and that temperature is trying to get into the home, having the 55 degree ground temp is good to allow the ground around the home to absorb the homes ever gaining heat. The opposite happens in the winter. If it is -10 degrees outside, the home is constantly taking in the 55 degree heat from the ground around the foundation. If the insulation level is higher than R-5, this cannot occur as easily. I look at this type of system as a built in Geo heating system. This is the reason I build my homes with an R-5 exterior insulation. By placing the foam insulation on the exterior, we move the condensation point to the exterior making the basement feel warmer yet. One last thing I recommend to my clients, but few do is to foam 4 feet away from the home to just below grade. This will prevent the frost from actually diving down on the homes foundation and keep the entire foundation wall at the magic 55 degree ground temp. This along with placing retaining walls in all areas that the foundation has taken a jump will keep your new home and its foundation working the most efficient way possible. I'm sure this is an area where many can and will disagree with me, but with my homes scoring on average less that 59 on the HERS Energy Star Scale it is hard to discredit.
One of the many topics this year that I had come from the people visiting my booth was regarding ICF foundations. Although many opinion may differ, they are not my choice for a couple reasons. The first being the added cost to the homeowner. In todays environment with appraisals being so difficult, this can be a factor right out of the gates for people. If the cost of the home is higher than the appraisal, other parts of the home need to be sacrificed in order to get the ICF's into the budget. The other problem I have with them is the mis-information on the efficiency. I think they are a great way to make a home efficient if they are taken all the way to the roof trusses(this is an extremely expensive way to use them), but if they stop at the foundation they are not. The State of MN has conducted studies proving that having more than R-5 insulation below grade is not necessarily a good thing. In MN, the average ground temperature is near 55 degrees all the time as long as it is below the frost line. 55 degrees can be good in the summer or the winter. I think of it this way. If in the summer it is 100 degrees outside and that temperature is trying to get into the home, having the 55 degree ground temp is good to allow the ground around the home to absorb the homes ever gaining heat. The opposite happens in the winter. If it is -10 degrees outside, the home is constantly taking in the 55 degree heat from the ground around the foundation. If the insulation level is higher than R-5, this cannot occur as easily. I look at this type of system as a built in Geo heating system. This is the reason I build my homes with an R-5 exterior insulation. By placing the foam insulation on the exterior, we move the condensation point to the exterior making the basement feel warmer yet. One last thing I recommend to my clients, but few do is to foam 4 feet away from the home to just below grade. This will prevent the frost from actually diving down on the homes foundation and keep the entire foundation wall at the magic 55 degree ground temp. This along with placing retaining walls in all areas that the foundation has taken a jump will keep your new home and its foundation working the most efficient way possible. I'm sure this is an area where many can and will disagree with me, but with my homes scoring on average less that 59 on the HERS Energy Star Scale it is hard to discredit.
Monday, February 7, 2011
Win a $100 gift card from Med City Builders this weekend!
Just a quick note to remind all of you about the Rochester Area Builders Home Show this upcoming weekend. I will be busy getting ready for this as well as heading off to tour the latest products at the Anderson Window plant this Wednesday. Therefore, I will keep the Blog this week short and sweet. This weekends event is a great opportunity for you to stop in to discuss your potential building plans or just talk about previous Blogs you have read. I plan on having plenty of previous homes interior and exterior pictures. I also carry a large book of previous home plans for you to get some great ideas. One of the activities I will be offering this year is a coloring contest for your children. I will be accepting the colored Med City Builders homes after the Home Show and will put the 3 finalists on my companies Facebook page. We will be announcing the winner through my website as well as Facebook. Your child can win getting the most "Likes" on his or her picture. You must only "Like" Med City Builders yourself in order to enter your child. More information will be given at the Home Show so stop by for details!
Last year, the traffic was really positive for us and we hope to see the same this year. I truly feel like there is a tremendous backlog of clients wanting to build a new home. The road block tends to fall in line with their existing home. Having success in the past and present with selling existing homes, I'd be happy to discuss this process with you at the Show as well. You may be surprised, but in talking with other Real Estate agents in the area as well as my own involvement we have really seen an upsurge in the existing market. So feel free to stop by to see all of the latest trends in the building industry, meet knowledgeable people in the trades, and discuss your current situation to see if now is a good time for you to make the move on a new home. To me, it seems like it was a less stressful way for you the client to interview the builders while meeting us at an event like this.
Last year, the traffic was really positive for us and we hope to see the same this year. I truly feel like there is a tremendous backlog of clients wanting to build a new home. The road block tends to fall in line with their existing home. Having success in the past and present with selling existing homes, I'd be happy to discuss this process with you at the Show as well. You may be surprised, but in talking with other Real Estate agents in the area as well as my own involvement we have really seen an upsurge in the existing market. So feel free to stop by to see all of the latest trends in the building industry, meet knowledgeable people in the trades, and discuss your current situation to see if now is a good time for you to make the move on a new home. To me, it seems like it was a less stressful way for you the client to interview the builders while meeting us at an event like this.
Tuesday, February 1, 2011
Start to finish. The process to get you there.
Today I'd like to discuss the basic principles behind my process in building a new home for my clients. One of the first steps in any project is to determine what it is that we are all trying to accomplish. My initial meeting with my clients typically revolves around trying to lay the foundation for what it is they really want to do. Many times they already have ideas of what they'd like to build and I then take these ideas and lay my foundations for what I'd like to present to the draftsman or architects. Most of the time, we start an idea from nothing more than a penciled drawing on a notebook. This is what a truly custom project is stemmed from and the most enjoyable way for me to create the vision. A typical timeline for getting the prelim plans back in hand can be less than a week depending on how complex the design is. Establishing prelims will now allow me to more accurately bid the home the way the client described to me in the first meeting. Once we have started to create the template for the specifications and the floor plans, we really start to dial in the pricing. We do this by beginning the selection process prior to signing any contracts. I like to take my clients on a one or two day tour to the vendors I have had the greatest success with. At this time, we really pin point the details of what is to be built into the new home. As we go through the process, I enter all the information into the book of information we create to organize the details. This book ends up being what is ultimately faxed to all of our subcontractors as well as placed on the job site for their review. Once this part of the process is completed, we incorporate the selections into the existing spec sheet and blueprint. This is when we get the project nailed down as far as the overall price. The best advantage I have found in doing the process this way, is it allows my clients to walk into the actual purchase agreement with near to exact pricing. Thus eliminating the need for change orders along the way. Once the purchase agreement has been signed, I am able to begin the finalization of the plans and ready them for permit.
Building begins once the lot is officially closed and the permit package is ready for pickup. Through this part of the process, I meet the clients at the site to determine the best placement for the home on the lot. As we begin the actual construction, I then develop the written schedule for the entire project. This allows the client, myself, and the subcontractors to be able to follow a timeline that insures completion dates are met. It allows the subcontractors to order in pertinent items that could have possibly held up the construction process. It also and most importantly helps you, the homeowner, to better understand the process and allows the homeowner to know what is being done on a particular day so they have the option of going to the job site to see progress being made. My major focus on any job I supervise is to always have activity regardless of what it is. On days where work is not being completed, it typically means that it is filled with inspections.
Once the new home is completed, we prepare the home for closing. As we have gone through the process, we have met with the clients along the way. As we get to the end, I set up pre-closing walk throughs to uncover any minor defects that can be taken care of prior to closing. This is typically done a week or so before closing. This allows us to have ample time to complete the work. As the closing date approaches, we also conduct a final inspection to insure all of the work is done to the home owners satisfaction. At closing, I furnish the homeowner with a packet of information discussing warranties, spec sheets, State warranties, the timelines for my 30 day post closing inspection, and the 1 year post closing inspection. These 2 last inspections are great ways for me to come back to the home and discuss any questions you as the home owner might have after you have settled in. Many times, it revolves heavily on the complex heating systems we install as well as the Energy Star ratings which I typically have in hand.
In a nutshell, our relationship with you begins at the first meeting but lasts many years after. I often tell my clients that we have just became married once we have signed the final agreements. As a builder, I'm responsible for portions of their new home in upwards of 10 years. I hope this helps better understand a typical building process in the life of one of my clients eyes.
Building begins once the lot is officially closed and the permit package is ready for pickup. Through this part of the process, I meet the clients at the site to determine the best placement for the home on the lot. As we begin the actual construction, I then develop the written schedule for the entire project. This allows the client, myself, and the subcontractors to be able to follow a timeline that insures completion dates are met. It allows the subcontractors to order in pertinent items that could have possibly held up the construction process. It also and most importantly helps you, the homeowner, to better understand the process and allows the homeowner to know what is being done on a particular day so they have the option of going to the job site to see progress being made. My major focus on any job I supervise is to always have activity regardless of what it is. On days where work is not being completed, it typically means that it is filled with inspections.
Once the new home is completed, we prepare the home for closing. As we have gone through the process, we have met with the clients along the way. As we get to the end, I set up pre-closing walk throughs to uncover any minor defects that can be taken care of prior to closing. This is typically done a week or so before closing. This allows us to have ample time to complete the work. As the closing date approaches, we also conduct a final inspection to insure all of the work is done to the home owners satisfaction. At closing, I furnish the homeowner with a packet of information discussing warranties, spec sheets, State warranties, the timelines for my 30 day post closing inspection, and the 1 year post closing inspection. These 2 last inspections are great ways for me to come back to the home and discuss any questions you as the home owner might have after you have settled in. Many times, it revolves heavily on the complex heating systems we install as well as the Energy Star ratings which I typically have in hand.
In a nutshell, our relationship with you begins at the first meeting but lasts many years after. I often tell my clients that we have just became married once we have signed the final agreements. As a builder, I'm responsible for portions of their new home in upwards of 10 years. I hope this helps better understand a typical building process in the life of one of my clients eyes.
Thursday, January 27, 2011
Happy new cabin owners!!!!
Below is a testimonial that we just recently received from one of our clients.
Greetings Andy,
I want to say thank you to you and your people for the excellent job you did with our cabin. So, please forward this letter to all of your people. First, a little personal history that will underscore my heightened appreciation for all you have done.
The past several months have been challenging for me as I was assisting my father with seeing mom through her final months of life. Mom passed away on December 27th following an intense battle with Multiple Myeloma. She endured five types of chemotherapy in less than two years and tolerated many weeks of daily radiation treatment. For mom the disease was both debilitating and extremely painful. As their only child living within 2,000 miles I did everything I could to help. I cooked them dozens and dozens of renal meals, cleaned for them, attended countless medical appointments, shopped, offered help with difficult medical and legal decisions and provided emotional support. My job, our home and children and the needs of my parents demanded enough time, energy and emotional investment that it was impossible for me to prioritize the cabin. I knew taking on this cabin build was risky during such a busy and difficult time. Building construction has the potential to be highly stressful. A bad construction experience for us could have been the virtual “straw that broke the camels back.” Fortunately, for me, that was not the case.
Therefore, I owe you all, and my husband Greg, my greatest thanks. You all went the extra mile and built a truly beautiful, cozy cabin.
Andy, Thank you for being the organized leader. Thanks for all of your insights and suggestions. Thank you for listening to us and honoring our needs and ideas. Thanks for your patience and flexibility. We could not have had the cabin we wanted without your willingness to continue working with us on the details. I appreciate the excellent choice in subs and the good relationship you must have with your subs as they did what you asked, what we asked. Thank you for doing the build so quickly, that still amazes me! Greg and I have high standards and Greg is both meticulous and highly intelligent. It takes a quality builder to satisfy us. You have succeeded. I would definitely do another build with your company.
Greg and Sharon, Long Lake
Tuesday, January 18, 2011
Spring is upon us!!!
This sounds a little crazy to post in the middle of January, but what a difference a year makes. Since December, I have seen numerous web leads and the same goes for the phone inquiries to build this upcoming spring. As it sits now, Med City Builders of Rochester has 3 new starts in the next 4 weeks! We also have several pre-sold custom homes for this upcoming March through May. All of this before the Rochester Area Builders Home Show and the Spring Showcase, which leads me to believe 2011 is going to shape up to be a great year. Thanks largely in part to the overwhelming influx of referrals from our loyal past customer base. Our hats go off to our past customers for that. With Spring coming earlier than normal this year for us, we urge you to start getting your building plans in order now. The 3 new homes we are soon to be starting have little to no frost in the ground, so it will make for ideal winter building conditions. So if you're in the market to begin the building process, feel free to drop us a line now. You can figure a month of preparation and another week or so to begin the process. That puts you at March 1 if we started the project today and the end of June for your new homes closing date! Let's get building!!!!
Wednesday, January 5, 2011
Expect lumber prices to spike in early Spring of 2011!!!
Recent sources indicate a spike in lumber prices nationwide are going to occur in the very near future of 2011. According to Pro Sales Online which is a well known trades web site for the lumber industry, we can expect this. According to a recent published report by Jim Haughey, Haughey believes one such spike will occur in lumber as housing starts increase; he expects they'll rise from an annual rate of around 600,000 today to 800,000 by year-end 2011. "A sharp price spike for lumber is likely in the spring or summer until additional mill capacity is restarted," he said. "The price surge will ebb after a few months, but prices will remain clearly above the pre-spike level."
Along with this a few words have buzzed in the industry with China and Russia no longer having as solid of a relationship as in the past. If this trend continues, China could start to purchase materials for their ever growing appetite for growth through other countries. One major candidate for these purchases could be just to the north of us, Canada. With Canada and the US currently having a smaller than average work force, the demand could cause prices to jump faster than predicted above. All hear say, but something to consider if even considering the thoughts of building a new home in the spring of 2011.
Along with this a few words have buzzed in the industry with China and Russia no longer having as solid of a relationship as in the past. If this trend continues, China could start to purchase materials for their ever growing appetite for growth through other countries. One major candidate for these purchases could be just to the north of us, Canada. With Canada and the US currently having a smaller than average work force, the demand could cause prices to jump faster than predicted above. All hear say, but something to consider if even considering the thoughts of building a new home in the spring of 2011.
Subscribe to:
Posts (Atom)